By Admin
MOLD
CAM3D of CADmeister creates data for machining curved surfaces for solid models and also for 3D CAD models that include surface data.
Users can display models on the CAD screen, and use them in order to calculate paths that can satisfy machining needs.
Furthermore, CAM3D creates paths for machining curved surfaces from various angles, provided that users have set tool axes.
Features
The command for Contour Offset Machining creates a path for roughly machining the contour of a model, provided that the cross-sections of the model have been processed by executing the "Offset" command.
- The command for Contour Offset Machining has a wide variety of capabilities such as of indicating Area Curves/Lines, automatically calculating paths and specifying solids on the basis of the data of modelled shapes. Thus, it enables faithful expressions of the shapes of materials.
- The command enables rough machining efficiently and reliably by inserting arcs into concave parts and trochoid paths into highly stressed parts.
- Any parts that have been left unprocessed can be automatically detected and machined through an intermediary processing.
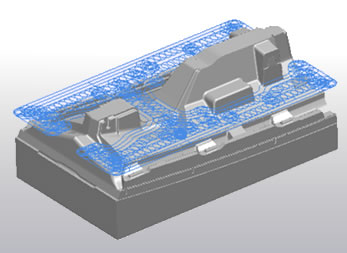
- Contour Machining for the Uncut Area
The command creates finishing paths for contour machining of a model.
- The command automatically detects flat areas, provided that a predetermined angle has been specified. It thus enables a concurrent creation of paths for machining along contours and those for machining flat areas.
- The command provides two methods of processing flat areas: 'Scan Machining' and 'Surface Machining'. Users can choose either of them in accordance with the purpose of machining.
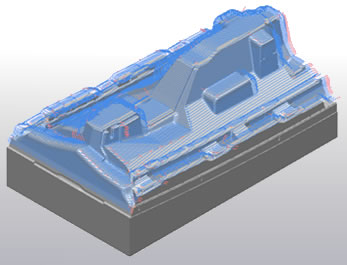
The command creates paths for finishing the machining of a model through the use of Scan Lines.
- The command enables users to machine a surface evenly, provided that profile lines have been indicated and paths have been created in order to machine any parts left uncut by the previous machining.
- There are two methods for indicating an area subject for processing: 'Tool Center' and 'Tool Touch Position'.
Users can choose either of them in accordance with the purpose of machining.
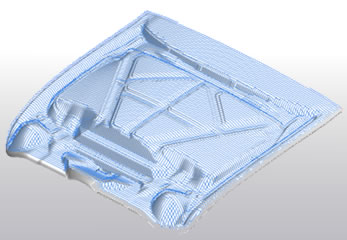
This command creates finishing paths that keeps a regular pitch of machining surfaces.
- This command creates a wide variety of paths for machining surfaces depending on the shapes of subject areas.
- The command creates paths that can smoothly change the blade position in order to round concave corners without acute bends.
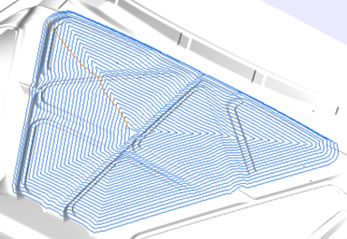
The command automatically detects any portions that have not been machined during the previous operation, and also creates paths for Corner Machining along ridges.
- The command creates paths for machining contours of a steep inclined surface whose tilt angle is a predetermined angle or more. It creates paths for a gentle slope. Thus, this command enables efficient machining for corners.
- The command reduces stress on tools, provided that the "Cutting" function is specified for the areas where there are many uncut locations.
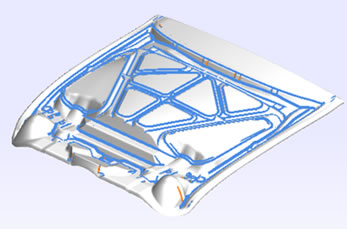
The command creates paths for finishing the machining of a model through the use of Scan Lines.
'Contour Spiral', 'Contour Guide', 'Ridge', 'Guide Machining', 'Line Projection', 'Area Projection'
Share this